Hazardous area lighting is a critical component of safety in industrial settings where there is a risk of fire or explosion due to the presence of flammable gases, vapors, liquids, or combustible dust. These areas can include oil refineries, chemical plants, coal mines, offshore drilling platforms, and marine vessels.
Hazardous area lighting fixtures are designed and certified to prevent the ignition of flammable substances and to operate safely in the presence of them. They are constructed with sturdy and durable materials and employ special features such as sealed enclosures, explosion-proof housing, and specialized lenses that help prevent sparks from igniting flammable substances. Read More ...
What types of Hazardous lighting are there?
There are two main types of hazardous area lighting fixtures: intrinsically safe and explosion-proof. Intrinsically safe fixtures are designed to be incapable of generating sparks or other sources of ignition, even under fault conditions. Explosion-proof fixtures are designed to contain an explosion within the fixture itself, preventing it from propagating to the surrounding environment.
All hazardous area lighting must demonstrate compliance to ATEX directives. In addition, they should provide assurance that the luminaire should not cause an explosion during routine operation. The specific type of hazardous area lighting fixture that is required for a particular application depends on the classification of the hazardous area. Hazardous areas are classified into zones based on the level of risk of explosion. Zone 0 is the most hazardous area, followed by Zone 1 and Zone 2.
Hazardous area lighting is essential for maintaining safety in industrial settings. It helps to prevent fires and explosions by providing illumination in high-risk areas and by preventing the ignition of flammable substances.
The below table summarises the definition of ATEX zones:
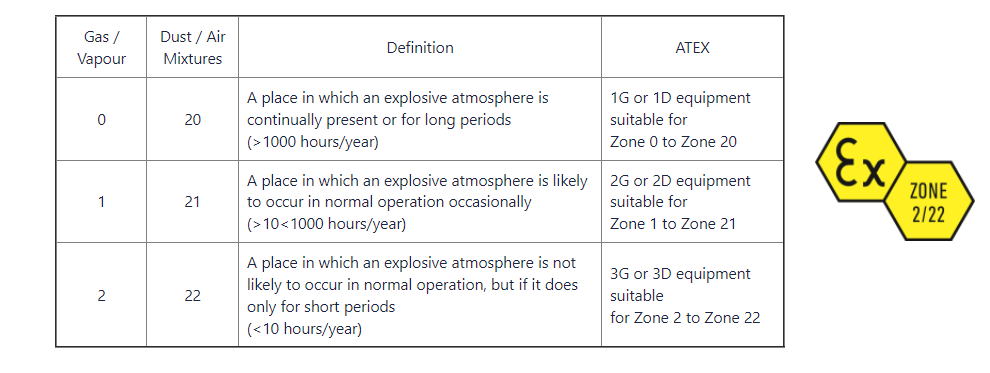